アルミ製缶板金VA・VE
アルミ板金とは
アルミ板金の用途
アルミは我々が生活する上で様々な用途に用いられます。特にアルミは工業製品としてよく使用される鉄やステンレスなどの材質に比較して、下記のような特徴があります。
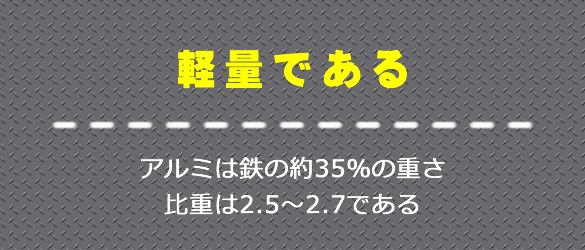
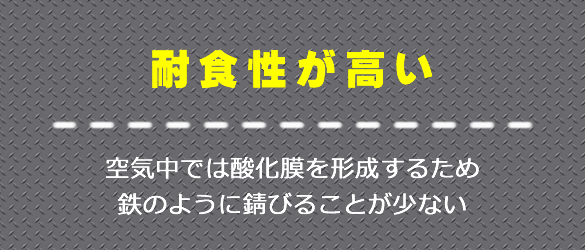
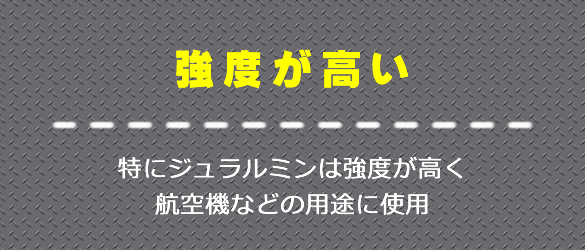
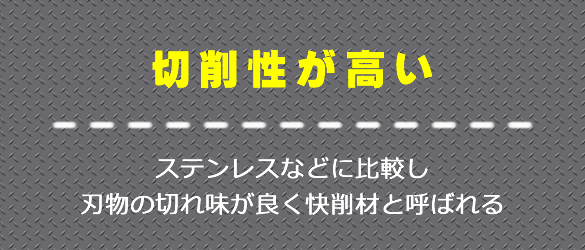
これらの軽く・強度があり・耐食性が高いという特徴を活かして、アルミによる板金加工製品は下記のような産業用の用途に幅広く使用されています。
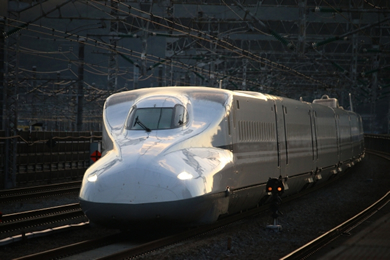
鉄道車両
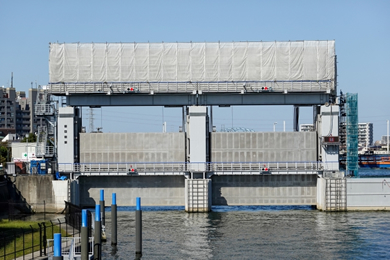
水門
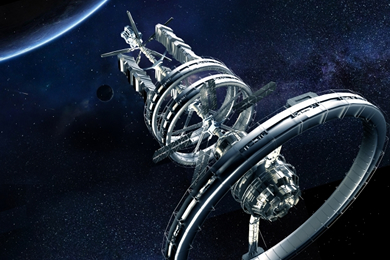
航空宇宙
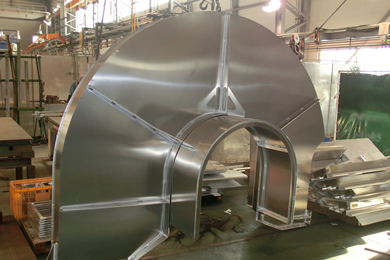
大型カバー
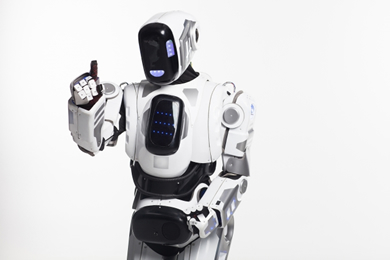
ロボット
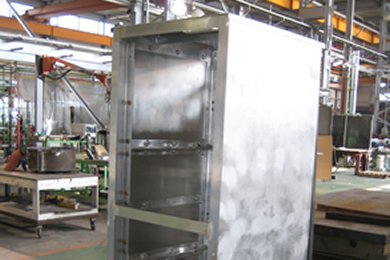
船舶用各種設備
アルミの特性
このように軽く、強度があり、耐食性が高いという特徴を持つアルミですが、一方で溶接などの板金加工や機械加工を行い場合にはその特性をよく知った上で行う必要があります。
また、鉄やステンレスなどとは違った定尺(寸法)で取引されているので注意が必要です。
各材質の機械的性質一覧
材質 | アルミ A5052 | アルミ A7075-T6 | ステンレス SUS304 | 鉄 SPCC |
比重 g/㎤ | 2.68 | 2.80 | 7.93 | 7.87 |
引張り強さ N/㎟ | 195 | 560 | 520 | 270 |
硬度 ビッカース硬度(Hv) | 50 | 170 | 200 | 105 |
※鉄やステンレスと比較し、約3分の1程度の軽さであることが分かります。
なお、上記のような機械的性質では現れにくい特徴のうち、アルミの精密板金・製缶板金に関わる部分としては、大きく下記の2点があります。
1.アルミは、溶接による熱によってひずみやすい
製缶を行う際に使用されるアーク溶接(一般的にはTIG溶接)では、そのアーク熱は4,000度~6,000度にまで至ります。
この熱によって母材・ワイヤーを溶かして溶接を行うことになりますが、当然、この非常に高い熱によってひずんでしまいます。
鉄は比較的ひずみが少ない金属になりますが、ステンレスはもちろん、アルミは少しの熱で大きくひずむため、溶接を行う際には注意が必要です。
2.アルミは、曲げ加工によって割れやすい
鉄やステンレスなどと比較すると、アルミはいわゆる「粘り」が無い材質になります。
したがってプレスブレーキなどで曲げ加工を行う際、鉄やステンレスと同じように鋭角に曲げを行うとヒビが入ったり、割れたりします。
したがって割れが起こらないようにRを付けて曲げたり、応力を分散させるような形で切り出すなど工夫が必要となります。
アルミ板金における設計者が押さえておくべきポイント
これまで見てきたように、アルミは軽くて強度が高いといった特徴がある反面、熱に弱く曲げ加工は難しいという、非常に扱いが難しい材質でもあります。
その中でも特に注意すべきポイントは溶接であり、溶接によって発生したひずみを除去する作業(ひずみ取り)は時間もかかるのでコストアップに繋がってしまいます。
したがって、このアルミを使用した製缶板金・精密板金においては、コスト上昇を抑えながら品質を向上させるための設計のポイントがあります。
1.溶接を無くす
アルミを用いた製缶板金においてコストを抑え、品質を向上させる一番のポイントは、溶接を行わないように検討を行うことです。
設計においては品質や強度を重視するあまり溶接を多用してしまいがちですが、これが逆に品質を損ない、コストアップとなってしまうことがあるので注意が必要です。
2.全周溶接を断続溶接にする
例えば鉄などの製缶板金などの場合、TIG溶接を行う際には全周溶接を行う事が一般的ですが、鉄よりもアルミは熱によるひずみが非常に大きく出るので、アルミの場合はできるだけ全周溶接とせず、強度的に問題ない範囲で断続溶接に切り替えることでコストを抑えることが可能です。
3.スポット溶接を採用する
通常、製缶板金を行う企業では保有していませんが、アルミ専用のスポット溶接機というものも存在します。
スポット溶接はTIG溶接よりも熱によるひずみが発生しにくいので、強度的に許容される場合は、スポット溶接を行うとコストダウンとなります。
4.熱のかからない、リベットやボルト・ナット固定する
まったくひずみが許されないような状況では、溶接そのものを行うことが困難になります。
そのような場合で部品同士を固定しなければならない場合、リベットによる固定や、ボルト・ナットによる固定など、溶接による熱をもたない固定方法を検討することも必要です。
ただし、TIG溶接やスポット溶接に比較すると、リベットによる固定は強度的に落ちるので検討が必要です。さらにボルト・ナットによる固定の場合は、多くのケースでは緩み止め対策を行います。
5.溶接する場所を端のほうにずらす、左右対称にする
アルミ溶接を行うことによって生じるひずみは、その熱が集中するところに生じやすいものです。したがって、設計上可能な範囲で熱の集中を回避するような構造とすることが、最終的にはコストダウンに繋がります。
例えば溶接を行う場所を端のほうにずらしたり、あるいは溶接を行うアルミのプレートが、片方のみに穴があいている場合には熱が一方に集中してしまうので、問題なければ左右均等に穴をあけることでひずみを低減させることが可能です。
6.熱の応力集中が起こるところを逃がす
上記5.とも関連しますが、いくら左右対称なものを溶接したり、端のほうに溶接位置をずらしたとしても完全に応力集中を回避することは不可能です。
もし、溶接によるひずみが集中する場所が明らかな場合は、その部分で応力を逃がすような対応、すなわち切り込みを入れたりするような検討も必要です。
7.板厚を厚くする
ひずみが大きく発生しやすいアルミ板は、その薄さが薄くなればなるほどひずみが顕著に現れます。したがってひずんでどうしようもない製缶品の場合でこれまで述べてきた対策をすべて盛り込んでも大きなひずみが発生してしまう場合は、板厚を厚くすることを検討します。 この対策は材料費が上がってしまうという反面、ひずみ取りにかかる時間とコストを低減させることができます。
なお、鉄やステンレスなどと比較し、板厚を厚くすることによるひずみ低減の効果が高いのもアルミの特徴になります。
このように、アルミ製缶板金では設計時に抑えておけば品質も向上しコストも低減できるポイントが多数あります。
この技術ハンドブックには、これらの設計者がおさえておくべきポイントを具体的に紹介しています。
技術ハンドブック
株式会社アコオ機工では、アルミニウムの板金・溶接及び組立てに特化して積み重ねてきた、ローコスト設計と信頼性・品質向上に役立つ技術を、1冊の本にまとめた「技術ハンドブック」を無料プレゼントしております。
ハンドブック内には、アルミの製缶板金加工に関するVA・VE事例をはじめとした設計・開発者様に、基礎知識など有益な情報を掲載しております。
技術ハンドブックをご用入の方は、下記ハンドブックプレゼントフォームよりお申し込みください。
ハンドブックの目次
1.アルミ板金におけるVA・VE設計のポイント
- アルミ板金はなるべく曲げ加工で製作できるように設計する
- アルミ板金は断続溶接の場合でも全周の開先加工を許容する
- アルミ板金の割れ防止切り欠き穴は溶接で埋めない
- アルミ板金は組立性を考慮して設計する
- ネジ締結からリベットへ変更することでコストダウンを行う
- 割れ易いアルミの曲げ構造は分割にて設計する
- アルミ製缶板金は穴・タップが曲げRにかからないように設計する
- アルミ板金は製缶後のタップ加工が必要ないように設計する
- 精度が高くない穴加工は集約して工数を削減できないか検討する
- 曲げ部への部品取り付けは、C面取りではなく部品自体を小さくする
- 長穴は手作業で穴あけ加工する場合、加工の手間がかからない形状を採用する
- アルミ製缶板金は、曲げ加工後の切り欠き工程が不要となるように設計する
- アルミ製缶板金は、加工工数が少なくなるように材質を選択する
2.アルミ板金の溶接・曲げにおける品質向上のポイント
- アルミ板金はなるべく一体化し溶接個所を減らす
- アルミ板金は溶接によるひずみを回避するため補強を入れる
- アルミ板金は溶接が少なくなるように形状変更を行う
- ひずみを回避するため溶接を行う部品はなるべく小さく設計する
- アルミ板金は溶接の作業性を考慮し溶接位置を指示する
- 小さなアルミ部品を溶接する際は十分な大きさを確保する
- アルミ板金はなるべくひずみが出ないように設計する
- アルミ製缶板金はガス抜き用の穴を考慮して設計する
- アルミ板金における角部の形状設計ポイント1
- アルミ板金における角部の形状設計ポイント2
- アルミ製缶板金は、割れ防止のためにワレ防止逃がし穴を設ける
- 曲げ部分が干渉する場合の形状変更のポイント
- アルミ板金は曲げ加工付近の割れ会費のためR形状とする
- アルミ板金における曲げ高さの限界値
- アルミ製缶板金は、曲げ加工後に寸法のズレが発生しないよう補強を組みこむ
3.アルミ板金におけるひずみを最小限におさえる設計のポイント
- アルミ製缶板金は、溶接からリベット構造に変更する
- アルミ製缶板金は、なるべく板厚を厚くしひずみを抑える
- アルミ製缶板金は、全周溶接ではなく断続溶接を採用する
- アルミ製缶板金は、ひずみが抑えられる箇所で溶接する
- アルミの製缶板金は、ひずみの少ないスポット溶接を採用する
- アルミ製缶板金においてひずみが集中する箇所は、あらかじめ切断する
- アルミ製缶板金は、ひずみを考慮しながらリブの採用を決定する
- アルミ製缶板金では、部品をなるべく左右対称になるように設計する
- アルミの製缶板金は、ひずみの少ない形鋼を採用する
- アルミ製缶板金は、ひずみ防止のために極力溶接を行わない